Multi-sensor, multi-channel, multi-parameter analyzers can greatly reduce the cost per point of any measurand including pH, residual chlorine, ORP, ozone, chlorine dioxide, dissolved oxygen and turbidity measurements without sacrificing the quality of those measurements.
The CRONOS® and CRIUS® controllers both allow the connection of multiple sensors. For example, a CRIUS® may be made up of multi-sensors of the same variety such as up to four chlorine sensors, or could be made up of a mix (multi-channel analyzer), such as a pH sensor, a chlorine sensor, and a turbidity sensor. Whatever your requirement for a multi-channel analyzer, the CRONOS® and CRIUS® ranges will provide what you need.
The CRONOS® is a high quality, low cost transmitter designed to give water treatment engineers everything that they need from a transmitter and nothing that they don’t. With no frills, costs can be kept to a minimum whilst optional communications packages allow Profibus, Modbus ASCII, Modbus RTU, Modbus TCP, 4-20mA analogue outputs, and relays for alarms and control.
The CRONOS® has the capability to control up to two sensors of any type with appropriate analogue outputs and relays. Equipped with optional PID control, the CRONOS® is very able to control complex water treatment processes at a fraction of the cost of other controllers.
The CRONOS® can also come in a multitude of languages making it suitable for use in any market.
Customers requiring additional functionality such as downloadable datalogging or remote access via the internet should consider the CRIUS® controller.
The CRIUS® offers more sensor connections, more functionality and more flexibility with a color screen and optional built in 3G modem. The CRIUS® is an attractively priced, top of the range instrument controller. Optional communications packages allow Profibus, Modbus ASCII, Modbus RTU, Modbus TCP and others.
The CRIUS® is equipped with the capability to connect up to four sensors of any type with appropriate analogue outputs and relays. Four sensors not enough? Simply connect up to 4 CRIUS® together all using the same display and communications. Equipped with datalogging as standard and multiple PID loops as options, the CRIUS® is very able to control complex water treatment processes at a fraction of the cost of other controllers.
The CRIUS® can also come in a multitude of languages making it suitable for use in any market.
Customers requiring a no-frills controller should consider the CRONOS® controller.
Industry 4.0 relates to the concept that we are living through a 4th Industrial Revolution where factories will be as SMART as they can be. The main principles are based on:
- Interoperability
- Information Transparency
- Technical Assistance
- Decentralization
Water 4.0 is how this technology and philosophy will be implemented/will affect the water industry. The Internet of Things refers to all devices we use all the time talking to each other and making their own decisions.
It is generally accepted that SMART refers to the increasing sophistication of equipment to make decentralized decisions, so it is this technology that allows for the implementation of Industry 4.0 or Water 4.0, and DIGITAL refers to its comms capability. For example, in 1990 a chlorine analyzer measured chlorine in water, gave out a 4-20mA output proportional to the chlorine and a couple of relays.
In 2018 the CRIUS® HaloSense (fully Water 4.0 developed) can provide the 4-20mA output and relays, but also has multiple digital comms options (interoperability), has space for up to 16 sensors (information transparency), has wireless and wired internet access (technical assistance) and full PID capability with remote setpoint, i.e. another device can set the setpoint (decentralization). Watch a 2 minute animated video about Pi’s CRIUS® controller below.
Get more info on any of our multi-parameter analyzers
Please contact us by using the form below.
- Low cost per point
- Process control options
- Remote access options
- Stable, reliable, accurate sensors
Multi-channel online analyzers from Process Instruments all maintain their level of functionality and include:
- 4-20mA outputs
- Assignable relay outputs
- Intuitive menus
- Text alarms to your mobile
- High resolution displays
- Graphing and datalogging
- 9 buttons for easy navigation
- Enclosure; wall, panel, pipe or pole mounting. IP65/NEMA 4x.
The CRONOS® and CRIUS® multi-sensor systems are equipped with process control options, relay outputs, serial communications, (TCP, Ethernet, Modbus and Profibus). In fact the multi-sensor systems have all the options you could want in an online analyzer whilst maintaining a low cost and great value for money.
Typical Configurations
- Multiple channels of pH, residual chlorine, turbidity, chlorine dioxide
- pH and chlorine
- ORP and chlorine
- pH and chlorine and turbidity
Summary of Applications
- Water Treatment
- Drinking Water
- Waste Water
- Pool and Spa Control
- Industrial Water
- Food and Drink
- Paper and Pulp
The CRONOS® is often used in applications where the remote access capability of the CRIUS® is not required. The CRONOS® is a universal controller capable of outputting a PID signal via an analogue (4-20mA) or a pulse width modulated relay (to control for example, an on/off pump). With the latest in communication options, the CRONOS® is capable of running Profibus, Modbus or TCP/IP via Ethernet.
The CRIUS® is preferred in the swimming pools market, where the superior control and sensor capability provides for better quality bathing water. Again the remote access is proving essential to our customers along with the Variable Speed Drive (VSD) control which is massively reducing electricity usage and CO2 emissions (and reduces electricity bills!).
In the municipal drinking water market, the superior control capability of the CRIUS® is making it the controller of choice for areas like coagulation control with the superior sensors in use, particularly for chlorine control and dissolved oxygen control.
Both multi-channel analyzers have a number of options available.
CRONOS® options include:
- Modbus RS485/LAN
- Profibus DPV 1
- PID/flow proportional controls
- Remote sensors
- Color display
- Downloadable data logs
CRIUS® options include all CRONOS® options plus:
- Remote access via LAN
- Remote access via 3G/4G
- Expandable to 16 sensors
Document | Type | Size |
---|---|---|
CRONOS® |
Brochure | 582kB |
CRIUS® |
Brochure | 584kB |
CRIUS® Remote Communications |
Brochure | 573kB |
CRONOS® and CRIUS® Control Options |
Technical Note | 520kB |
Water 4.0, Industry 4.0, IoT, SMART and DIGITAL |
Technical Note | 596kB |
How To Specify a Pi Analyzer |
Technical Note | 627kB |
Remote Access GPRS |
Technical Note | 554kB |
PID Control |
Technical Note | 541kB |
Focus Ons are a series of short articles distributed by email providing technical information regarding instrumentation, process measurement in potable, waste, process and pool waters. If you would like to join the mailing list, please contact us.
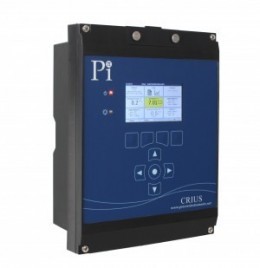
…Pi’s CRIUS® controller is already set up for all these things?
…Pi already has SMART and DIGITAL installations all over the world?
…Pi works as partners to many multinational organizations to provide their remote access, remote comms and SMART technology?
So what is Industry 4.0 (and Water 4.0 and the Internet of Things and SMART and DIGITAL technology)?
Simply put the concept is that we are currently living through the 4th Industrial Revolution.
The first was mechanization, (what we currently think of as the Industrial Revolution), so steam engines, Spinning Jennies, railways, canals and factories in the 1800’s.
The second was the age of mass production so; electricity, the production line, etc., largely in the first half of the 20th century.
The third was computers and automation, in the latter part of the 20th century, and the fourth?
The fourth (Industry 4.0) is about ‘SMART’ factories. (The original use of the expression Industry 4.0 was by a group of advisors to the German government who presented their advice in 2012). Industry 4.0 is about making factories as SMART as they can be. That is having assets (machines, people, robots, AI, cyber technology etc.) all communicating with each other.
The main principles put forward were based on;
- Interoperability – everything should be able to talk to everything else.
- Information Transparency – the physical world should be able to be recreated virtually to allow for testing and modelling.
- Technical Assistance – information should be presented in a way that supports people to make good and fast decisions.
- Decentralization – after decades of centralization to things like DCS systems and SCADA systems, the future is to enable as many decisions as possible to be made locally by whatever intelligence (human or machine) is available.
So what is Water 4.0 and SMART and DIGITAL?
Water 4.0 is simply how this technology and philosophy will be implemented/will affect the water industry. There are some clear outcomes from the above… more sensors… more modelling… ‘SMARTER’ instruments, controllers, pumps etc.
SMART and DIGITAL.
These terms aren’t quite as well defined as others. Generally it is accepted that SMART is the increasing sophistication of equipment to make decentralized decisions. For example, in 1990 a chlorine analyzer measured chlorine in water, gave out a 4-20mA output proportional to the chlorine and a couple of relays.
Now the CRIUS® HaloSense (fully Water 4.0 developed) can provide the 4-20mA output and the relays, but also has multiple digital comms options (INTEROPERABILITY), has space for up to 16 sensors (INFORMATION TRANSPARENCY), has wireless and wired internet access (TECHNICAL ASSISTANCE) and full PID capability with remote setpoint, i.e. another device can set the setpoint (DECENTRALIZATION). So SMART technology is the technology that allows for the implementation of Industry 4.0 or Water 4.0. DIGITAL tends to refer to the comms capability.
So what is the Internet of Things or IoT?
When the previous Industrial Revolutions happened, the technology and concepts spilled over into the consumer world from the business/manufacturing world. With Industry 4.0 it is beginning to be the other way around with consumer demand for the internet, and mobile phone technology, driving the technology. If we assume that in this Industrial Revolution the same thing will happen, then the Internet of Things refers to all devices we use all the time talking to each other and making their own decisions.
Imagine your mobile phone waking you at 6am and telling your kettle that turns itself on at 6.20am, which tells your car that starts itself and defrosts the windscreen at 6.30am etc., etc..
Not convinced that we are in a new Industrial Revolution?
Consider this…… perhaps Industrial Revolutions are only identifiable in hindsight?
And what does it matter? Well from Process Instruments’ point of view, it doesn’t. As long as our products are leading the way in providing our customers with what they need to enable their own Industry 4.0.
Any questions?
Please contact us by using the form below.
Pi’s controllers have always given flexibility but did you know that Pi’s new controllers can accommodate up to 16 sensors of any description?
This Focus On describes the 10 most popular innovations to be found in Pi’s new CRONOS® and CRIUS®.
No. 1 – Human readable service log
Both the CRONOS® and CRIUS® analyzer/controller has a downloadable human readable service log – giving an entire history of the instrument including current settings, calibrations etc. Provides a great snapshot of how an engineer left an instrument.
No. 2 – Cloning facility
Ever had to set up many instruments with the same settings? Simply set up one and copy it to others!
No. 3 – On screen wiring diagrams
Lost the manual or can’t be bothered to find it? Pi’s analyzers have the answer!
No. 4 – Want a bit more info on what’s going on with a sensor?
Pi’s new sensor maintenance pages are just for you then! Detailed information about all aspects of the signal coming off the sensor clearly available.
No. 5 – Instrument datalogs not quite giving you what you need?
Pi’s new look datalogs in CRONOS® and CRIUS® (downloadable) let you datalog almost everything, put graphs on the display, datalog the same parameters at more than one interval and a whole lot more. Never has instrument datalogging been so easy and complete.
No. 6 – New enclosure
The new enclosure brings a new level of flexibility being wall mountable, pole and handrail mountable and even flush mountable. Not only that, but it gives you loads of room to work in and there are even spare live, neutral and earth terminals to make wiring relays easier!
No. 7 – Not enough I/O?
Don’t worry, simply daisy chain 4 CRIUS® together and you can use the same display, comms options etc. and increase your I/O fourfold to give up to 16 sensors.
No. 8 – Bored of reading about stuff in manuals that you don’t have?
Pi’s new manuals are bespoke to each instrument. The manual is ‘built’ to match each individual instrument so the manual only has what you have!
No. 9 – Has the operator been messing with settings they shouldn’t?
No more! With 20 individual user settable logons, you can give people access to what they need and no more.
No. 10 – Control algorithms
Pi has developed a reputation for developing great control algorithms and this has continued with the new CRONOS® and CRIUS® with the introduction of feed forward control algorithms and a master controller which selects the correct control philosophy to use (for use with complex systems such as coagulation control).
…nearly everything you can do in front of the analyzer you can do remotely?
…we have been working closely with our customers to bring you an even better service?
…a lot of our customers have seen the number of engineer callouts drastically reduce, saving them time and money?
Pi’s sleek and modern Remote Access solution
Pi has always been a leader in developing new technology and have had a remote access system for 10 years! The latest iteration of remote access is now a key part of our solution toolbox. Here are some of the features of our remote access:
User interface – The interface mimics the analyzer, making the data and other features easy to find. Anyone already familiar with the CRIUS® analyzer will already be familiar with remote access. Anyone requiring training can now be trained remotely using remote access and Skype.
User control – Each user has their own customizable access rights for what they can view and change on the analyzers. This is set by the ‘parent’ user.
Speed – The service now runs around 50 times faster than its predecessor, allowing users to connect and download the current sensor values and settings in under 30 seconds (test performed on CoagSense coagulation controller with 27 different devices such as sensors!).
Reduced data costs – By making the connection between the server and analyzer more efficient, Pi has reduced the amount of data required for nearly all tasks thereby significantly reducing costs.
Customer branding – On request, Pi can brand the remote access theme to promote a customer’s brand.
Data analysis – The graphical interface is a powerful and flexible tool for viewing your sensor data. The way we handle your analyser’s data means that every single data point is stored in the cloud, allowing a user to download 3 months’ worth of data with a single click.
Password reset – If a password has been lost or forgotten, a user can enter their email address into the password reset function which will then email a list of instructions on how to reset it.
Data limit – Users can now limit how much data each analyzer can use per day, meaning no more unexpected data costs.
So what can Remote Access do for you?
The remote access service has always been designed to save you time and money by allowing you access to the analyzer and its data from anywhere in the world. Now remote access can assist as a tool in doing a lot more:
- Remotely checking and changing settings for customers who may not be confident in doing so or who may not have access to the analyzer.
- Allowing Pi’s service team to temporarily remotely connect to the analyzer if customers have an issue and are unsure about how to solve it.
- Automatically sending daily/weekly reports of data logs and/or status logs to users from the server (no mobile data costs from the analyzer).
- Easily view when maintenance is required or due on analyzers, allowing users to efficiently plan which sites to visit and when.
- Know when alarms activate on the unit within seconds by enabling text and/or email alerts direct from the analyzer.
- Tune control values to optimize dosing without the need to visit the site.
- Analyze stored data to investigate incidents, explain issues or validate the process.
- Save money by reducing the number of callouts and the number of miles your engineers travel!
But what about security?
When the analyzer and remote access server communicate, Pi uses a ‘Pre-Shared Key’. This creates a secure connection between the server and analyzer. The key acts as a password and without it the analyzer will not respond. The key is randomly generated in every analyzer making it unique to each, and if required the key can be re-generated from the analyzer. The analyzer can also be connected directly to a Virtual Private Network (VPN) which blocks unwanted traffic and connections automatically and will only transfer information between the analyzer and server.
How does user access work?
Each user has their own username and password. This means that what they see and what they can do can be customized so only authorized users can make changes.
How are the analyzers and customers managed?
If a user creates a group, then they become that group’s ‘parent’. The ‘parent’ of a group creates the analyzers and users for that group. If a user is a ‘parent’ to more than one group, they will also have the ability to create users that can access multiple groups from a single user account.
… that PID can save you money by offering better process control?
… that PID can help you maintain a setpoint, even with a variable process?
… that the days of over complex and confusing PID are over?
… that Pi can tailor a PID system to your exact requirements? You may never have to touch those settings again!
In this Focus On, Pi would like to introduce you to PID if you haven’t come across it, and discuss some of the useful advanced features of modern PID systems, like on Pi’s CRONOS® and CRIUS® models for those more familiar with PID.
What is PID?
PID is a mathematical tool created by engineers and is used in controllers. It is a feature often found in industrial controllers and is available in Pi’s controllers, as an inexpensive upgrade.
What is PID for?
The best way to explain what PID does, is to take an example. Most people have been to a swimming pool at some point in their lives, so this is the example we shall use. PID is also applicable in a huge variety of other processes. If you are not sure, you can always contact us to discuss your application.
When a person enters a swimming pool, they create a chlorine demand. They do this by introducing sweat, bacteria, organic molecules and other substances into the pool water. Chlorine reacts with these substances, which results in chlorine being used up and the chlorine level dropping. The chlorine level in this example, is often called the process variable or PV in the context of PID.
In order to maintain a concentration or level of chlorine, more chlorine needs to be dosed. If you dosed the same amount of chlorine per bather, the level would not be stable as all bathers create a different chlorine demand (e.g. swimming for fitness produces more sweat than swimming recreationally). Dosing manually brings in the issue of human error, and how operators approximate or calculate the amount of chlorine to dose based on current levels. Another issue with manual dosing is that it is not a continuous process, meaning it is unlikely a stable level will ever be reached.
What does PID do?
PID takes the measured level of chlorine or the PV and compares it to the desired level or set-point. This comparison gives the error which PID interprets and then calculates an output. The output is an electrical signal which controls the dosing of the appropriate chemical. The output can control heaters, dosing pumps and many other mechanisms that can be used to change the PV.
How is PID used?
PID is made up of three parts, proportional, integral and derivative. Understanding what each part does helps operators choose the level of control best suited to them.
Proportional
– Is the most commonly used for portion PID and suits most applications. When using proportional control, the further away the measured value is from the setpoint, the larger the output will be from the controller. This is an appropriate level of control for most processes, and users can gain a lot of control from a purely proportional system.
In some systems where the PV is lost to the process, e.g. chlorine from a pool, heat from a boiler etc., the proportional control never quite catches up with the setpoint. Users can see that although the process approaches the setpoint it rarely, if ever, gets to it. This is known as ‘droop’. The user can compensate for droop if the removal of the PV is fairly constant, simply by raising the setpoint, e.g. evaporation of chlorine from an empty pool. If droop changes often, (e.g. bather load or chlorine demand) then to eradicate the ‘droop’ then the integral part of PID can be applied to the signal to correct it.
Integral
-The output from the integral term is determined by both the magnitude and the duration of the error. A small error over a long period of time will trigger a larger response than from a purely proportional system. This helps the elimination of the ‘droop’ seen in processes with continuous loss, and also serves to help reach the setpoint quicker.
Derivative
–Derivative gain is rarely used and is generally set up only by expert engineers. Derivative gain uses the rate of change in the PV to try and predict future errors. This type of control is particularly susceptible to overcompensating, especially if there is even a small amount of signal noise (usually seen as spikes in the PV). Derivative gain is generally a tweak used by engineers to improve an already tight control, and is almost never used as an essential part of control.
What are the benefits of PID?
When properly set up, PID can lead to far tighter process control, which in turn can save you time and money. As an example, pool managers want to keep chlorine levels low, to improve the bathing experience and also save on chemicals. AquaSense is a chlorine analyzer system that responds quickly and appropriately to a change in bather load (also known as chlorine demand). This means pool operators can save money whilst maintaining the safety of the pool. PID can also help reduce the risk of overshooting the desired setpoint, reducing the risk of dangerous overdosing of the chemicals.
Advanced Features and Safeguards
Whilst maintaining a setpoint with a PID loop is a huge advance over using threshold relays to maintain an upper and lower limit, it is sensible to control the loop with extra safeguards, such as:
- Maximum and minimum pump outputs. This is mainly used to prevent the controller from employing too aggressive a control, which can lead to overdosing. A minimum output can also be used in a system where the measured parameter is lost over time, to prevent the controller ever turning the dosing off.
- Ramp rate is a proportional control that allows users to choose how quickly or slowly the controller doses, in order to reach the setpoint. It is especially useful on startup, and can prevent the controller dosing too quickly.
- Wind up protection is an integral control, which limits the duration aspect of the control. This puts a limit on how much previous error can accumulate. Without wind up protection, there could be a very large integral value, if the process ever reaches zero or on startup.
These are all standard features in all Pi PID controllers.
Conclusion
In summary, PID is a very useful tool when used correctly, and can result in significant chemical savings, not to mention reduced pump wear and tear and lower electricity costs.